Keynote Speaker 1
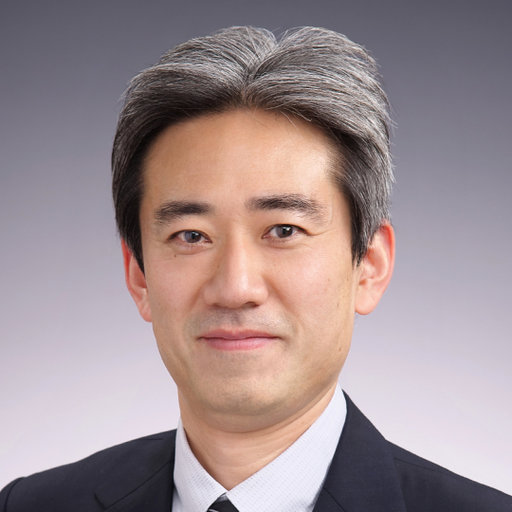
Title: Novel Ion-Conductive Polycarbonate-based Electrolytes for Battery Applications
Abstract Ion-conductive solid polymer electrolytes (SPE) are promising materials for energy storage devices, such as lithium rechargeable batteries, because they potentially have high safety and high manufacturing workability. Most studies on SPE have focused on the use of tpolyethers, such as poly(ethylene oxide) (PEO), however, studies have shown that there is an apparent limitation of the polyether-based electrolytes. In the present study, we considered the ion-conductive and electrochemical properties of SPEs consisting of polycarbonates such as poly(ethylene carbonate) (PEC) with Li salt. Previous studies have shown that certain PEC-based electrolytes exhibit a continuous increase in ionic conductivity with increasing salt concentration, and have very high lithium transference numbers. We revealed that highly aggregated coordination structure between carbonate groups and Li ions and anions based on the relatively rigid structure gives rise to the unusual characteristics, by means of spectroscopic studies. Furthermore, the study demonstrated possibility to take advantage of a high oxidation stability and a prevention effect of metal corrosion reaction, which are based on the highly salt-concentrated nature of the electrolytes. The favorable electrochemical properties potentially enable operation of lithium polymer batteries which need to be charged above 4 V. Moreover, we recently focus on the chemical structure of polymer framework for the development of ion-conductive properties of SPE. Copolymerization of carbonate and ether units was carried out for obtaining homogeneous electrolytes without phase separation showing excellent Li ion- conductive properties. The random copolymers of ethylene oxide with CO 2 (poly(ethylene carbonate/ethylene oxide), P(EC/EO)) containing lithium salt exhibited ionic conductivities and Li transference numbers (t + ) higher than 0.4 mS cm -1 and 0.6 at 60 ºC.Keynote speaker 2
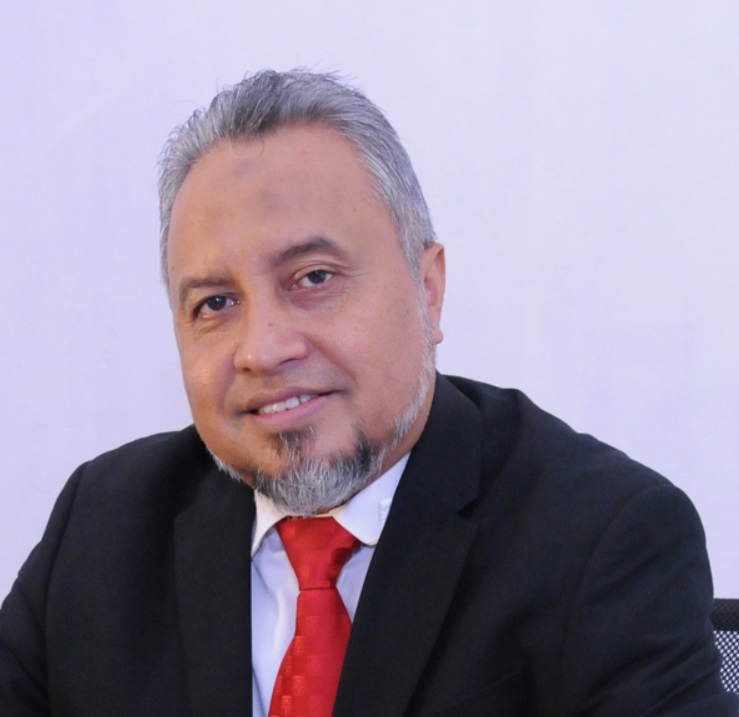
Biography
Che Hassan Che Haron is a Professor at Centre for Engineering Materials & Smart Manufacturing, Faculty of Engineering and Built Environment at the Universiti Kebangsaan Malaysia. He is currently the Deputy Dean for Research and Innovation. He is also the Head of Cluster for Advanced Technology and Smart Manufacturing Cluster and Research University Committee Member at Kementerian Pendidikan Malaysia. He is also MyRA Task Force and auditor for KPM. He was the Director for Research Management Centre in UKM. His research interests are in the manufacturing and productions engineering, specifically, in machining, cutting tool technology, tribology and machinability of difficult to machine materials such as titanium, Inconel 718 and composite materials. He also involved in wear of cutting tools, chip formation and the application of response surface methodology for design of experiment. He has published more than 200 journal articles and conference papers. He has obtained 5 patents and 1 industrial design.
Title: Sustainable Machining of Inconel 718 Alloy: Dry, MQL and Cryogenic Cooling
Abstract
Sustainable machining can be defined as the manufacture of products by a subtractive process by cutting action of a tool that is nonpolluting and minimizes damage to the environment and humans. For this reason, new clean technologies and proposals of work methods are required; they have to integrate the ecological and social dimensions at an operational level in the manufacturing processes. Inconel 718 is a nickel-based alloy which is mainly applied in the aircraft industries due to its high strength and excellent thermal and corrosion resistant. It is also known as difficult-to-cut material due to its abrasive, work hardening and low thermal conductivity characteristics that contribute to the high generation of heat and friction during cutting. The use of coolant is known to be one of effective method to facilitate the heat dissipation from the cutting zone. Recent trends in metal cutting shows the increasing of demand at the global stage for the application of eco-friendly machining approaches in order to eliminate the adverse effects of conventional cutting fluids. This experimental work was conducted to evaluate the performance of sustainable cooling techniques of cryogenic carbon dioxide (CO 2 ), Minimum Quantity Lubrication (MQL), cryogenic liquid nitrogen (LN 2 ) and dry cutting on machinability of Inconel 718. For the cryogenic CO 2 approach, a new concept of cryogenic cooling technique was introduced for efficient and consistent cooling performance. The results displayed cryogenic CO 2 is more effective in improving cutting force and surface roughness compared to others. As compared to cryogenic LN 2 and dry cutting, cryogenic CO 2 managed to reduce cutting force by almost 55% and 57.5% respectively. The slight difference of cutting force between cryogenic CO 2 and MQL by only 5.2% showed the remarkable role of the lubricant to reduce friction at tool-chip and tool-workpiece interfaces. However, for the surface roughness, the cryogenic CO 2 exhibited superior improvement as it is 41.4%, 12.6%, and 62.8% better than MQL, cryogenic LN 2 , and dry cutting respectively. Thus, it can be said that the adequate and consistent cooling effect by the coolant is more effective to disperse the generated heat and provide a significant influence on the cutting force and surface quality as both of them are heat-dependent. Nevertheless, the benefits of these machining approaches require more in-depth studies including the economic and practical aspects since some approaches require a substantial initial system investment.